AS Business Studies 9609
Business Studies – 4.1 Nature of Operations
- Transformation Process – The stages of production (inputs to outputs)
- The factors of production – Land, Labour, Capital and Enterprise
- The concept and importance of added value
- Efficiency, productivity and sustainability
- The impact of sustainable operation (labour and capital intensive)
4.1 The Transformation Process
The nature of operations is often referred to as production management. Production is the transformation of inputs (raw materials) into outputs (products).
Operations management decisions involve making effective use of resources (inputs), land, labour and capital to provide outputs in the form of goods and services by using a transformation process. Production can be done at primary, secondary or tertiary levels. Operations management seeks to ensure that goods or services are made with the required quantity, standard and in the most efficient manner. As such operations management is responsible for acquiring and allocating the necessary inputs and utilising them in such a way as to maximise output.
The transformation process is all the activities a business uses to transform inputs into outputs (products). The transformation process will add value to the inputs as value is added by the business transforming inputs into products.
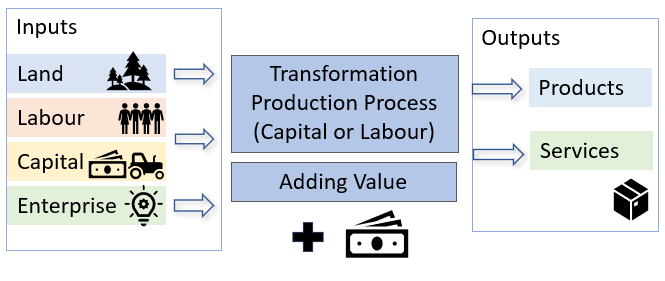
The method of production a business uses depends on the scale of the production, the type of product and available capital or resources. It’s important to understand the difference between each method of production and be able to recommend an appropriate method of production.
The objectives of operations management often include:
- Produce goods and services for its customers effectively.
- Control the transformation process to be efficient and add value.
- Cost-effectively procure appropriate inputs.
- Effectively manage an appropriate inventory level.
- Focus on quality, speed, flexibility, and the cost of production.
- Achieve an effective labour/capital production mix.
- Incorporate the latest technological approaches
Job production is where one item is made at a time, usually by skilled employees. Job production is chosen when the product needs to be made to meet the individual needs of a customer.
Operations planning is concerned with;
Which resources are needed to complete the production
How the work or processes will be organised and scheduled?
Who will perform the work?
Methods of production include
Job Production – Made to meet the customer’s needs
Batch Production – Making more than one at a time
Flow production
Mass Customisation
Batch production is used when a small number of identical products are made at the same time. Each batch goes through one stage of the production process before moving to the next stage. A good example is making batches of shirts for medium, large and small. Bakeries will also bake in batches of twelve, twenty-four or more depending on the oven size and product.
. .
.
Involves making individual products from start to finish. Each product is different and meets the unique requirements of the customer. Job production is often used by hairdressers, wedding dresses or wedding cakes.
Because the product is unique and bespoke the business can often charge higher prices as the product meets customer specifications.
Job production results in high-quality products as each product is made by skilled employees one at a time.
- Job Production can be expensive as workers tend to have higher skills and therefore higher wages.
- Time-consuming as completion takes longer due to greater attention to detail and higher quality products. As products are made for a specific purpose replacements can be difficult to source.
Exam Tip
The focus of operations management is to ensure that students understand the various production methods used by businesses. It’s important to practice applying your knowledge in context to the advantages and disadvantages of using various methods of production
Exam Tip
It’s important to remember that flow production can enable a business to gain economies of scale. Job production is less likely to help a business achieve economies of scale. If you are unsure how economies of scale work, take a look at the topic.
Flow production is where products are produced continuously using a production line. Partly finished products (goods) flow along the assembly
line with parts being added throughout the process. Think golf balls, cars or Coca-Cola.
The advantage of flow production is that a high number of products can be made at a lower cost. Because production can continue 24/7 and businesses can benefit from economies of scale. This means that the average cost per unit can be lowered.
.
4.1.2 Efficiency, productivity and sustainability
Definition of Kaizen
Kaizen is the continuous incremental improvement of an activity to eliminate waste.
Efficiency and Productivity.
Operations managers must consider choosing methods of production that make the best use of resources. By choosing the best method of production businesses can become more efficient as the potential waste is lowered. Increasing efficiency reduces waste as the business becomes more efficient more output can be made with the same amount of input. This also results in the business operations becoming more sustainable.
Increasing productivity can be done by the business making more output (products) per hour. If a business increases the productivity and also increases the inputs then only productivity has been increased and the operations have not become more efficient.
Labour or Capital-intensive
Measuring Labour Productivity
Economies of scale
Economies of scale refer to the cost-saving advantages that a business can gain by expanding the scale of production. Economies of scale allow a business to make things cheaper because they are bigger. The effect is to reduce the average cost per unit of production. Economies of scale are divided into internal and external.
Section A 4.1 Nature of Operations Practice for Paper One
Section B 4.1 Nature of Operations Practice for Paper One
Students are also Interested in:
32 Courses • 702 Video Tutorial
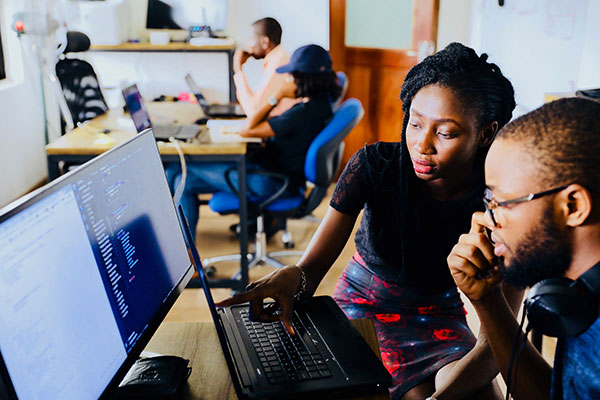
Digital Marketing Analytics
11 sections • 28 lecture • 19h 33m total length
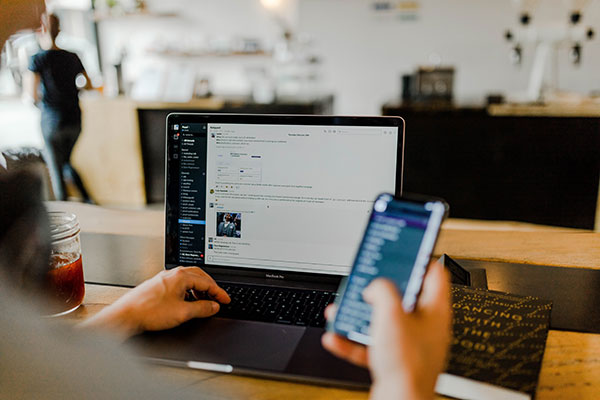
Marketing in a Digital World
11 sections • 28 lecture • 19h 33m total length
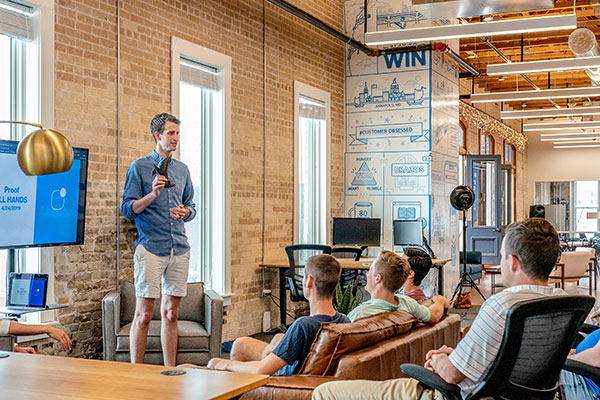
Marketing Analytics in Theory
11 sections • 28 lecture • 19h 33m total length

Range of Business Topics
Lorem ipsum dolor sit amet, consectetur adipiscing elit.

Expert Teacher
Lorem ipsum dolor sit amet, consectetur adipiscing elit.

Unlimited Access
Lorem ipsum dolor sit amet, consectetur adipiscing elit.
Get Additional Business Studies Resources!
Get access to additional business studies resources including sample questions and detailed examination feedback.